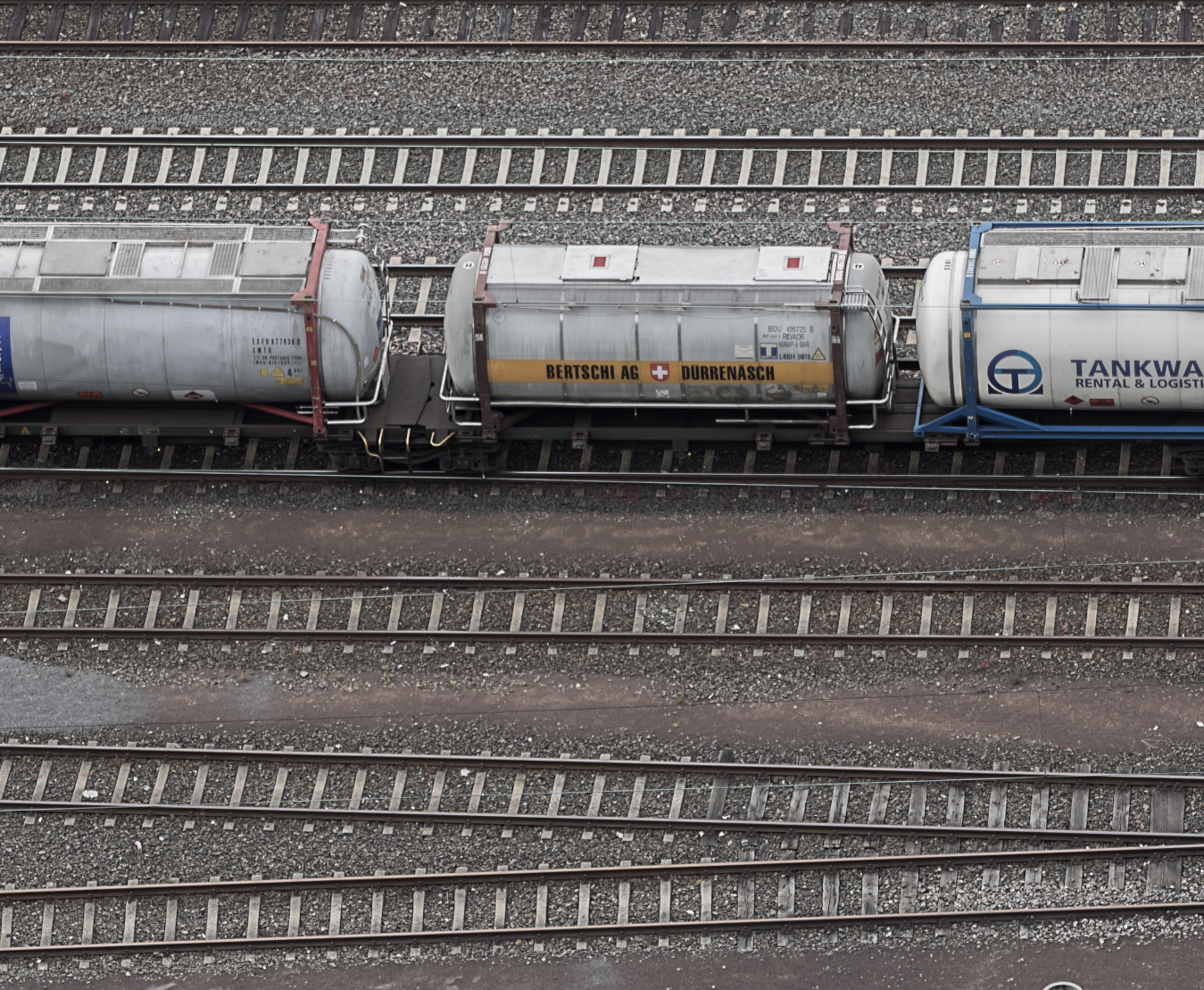
Patented measuring method
NextSensors based on the inverse magnetostrictive effect (also known as the magnetoelastic effect or Villari effect) are used successfully in many areas of industry. At Bayern Engineering, this effect was used for the first time to develop a dynamic rail scale.
The use of the inverse magnetostrictive effect in a dynamic rail scale offers considerable technological and, above all, practical and economic advantages compared to previous state-of-the-art measuring methods. This innovation is what makes efficient and economical weighing possible.
According to the current state of the art, there are essentially two economically relevant technological approaches to realizing dynamic weighing:
Both methods require considerable intervention in the track and/or special preparation of the rails for installation. Both methods usually involve a rail cut. Interrupting the continuity of the rail results in various disadvantages and restrictions on the use of the track in question.
The track scale from Bayern Engineering based on the magnetoelastic effect does not have the limitations of the above-mentioned measuring principles and offers further decisive advantages.
According to the Villari effect, ferromagnetic materials - such as a railroad track - change their magnetic properties under load. We have developed a sensor that measures this change, triggered by the force exerted on the rail as a train passes over it. This allows the weight of the train to be determined reliably and accurately.
The great advantage of this non-contact measuring principle in the technical sense is that the rail itself becomes the so-called primary sensor. The sensor from Bayern Engineering is simply clamped to the rail. The advantages:
The measuring error of the scales is currently less than 1 % under defined conditions - overrun speed up to 10 km/h and without active acceleration or deceleration. Due to the fast response behavior of the measuring principle, weighing at significantly higher speeds is also possible in principle.
A basic distinction is made between static and dynamic weighing. In static weighing, the vehicles are uncoupled, placed individually on a scale and weighed. This is time-consuming and impractical for complete weighing as part of efficient logistics processes.
Dynamic weighing has become established in order to put the benefits of weighing in relation to the time required. Here, the entire train is weighed as it passes over a measuring point.
The use of the inverse magnetostrictive effect in a dynamic rail scale offers considerable technological and, above all, practical and economic advantages compared to previous state-of-the-art measuring methods. This innovation is what makes efficient and economical weighing possible. The process for obtaining verification capability has been started.
The weight data can be imported seamlessly into the trenpex system. The weighing data is made available both via the trenpex Data Hub using the web portal and via the REST interface to further processing systems (ERP, TOS, etc.) together with the actual data generated by trenpex using OCR gates and AI processes. The advantage lies in the fully automatic weighing without the need for a weighing order or manual assignment of full to empty weighing.
For visual documentation and identification, the train is recorded with a camera system specially developed by trenpex. The system requires only a small distance to the track (60 cm) and can therefore also be installed between adjacent tracks in order to seamlessly detect traffic on neighboring tracks.
Vehicles on public rail networks usually carry a UIC number. This is automatically recognized on the images and the vehicles are thus identified. In closed, private networks such as in mining, industrial parks or ports, there are also vehicles without a UIC. These vehicles can be provided with a stick-on 2D code. This code is also automatically read and recognized from the images for identification purposes.
The downstream image processing generates a high-resolution image of each individual vehicle. This allows numerous details to be recognized, such as lever and valve positions or damage and soiling.
With the appropriate configuration of the system, trains up to a speed of 250 km/h and even in complete darkness are displayed in sharp focus.
Find out moreIf you have any questions about our weighing sensor or our company, please contact us. Simply write to us at info@bayern-engineering.de or send us your message using the contact form below.